Tea Plant Automation
Globalization is here to stay whether we are ready or not. Consumers will also demand products and services which are on par with the ones available anywhere in the world. The ability to adapt to this change on time will make the difference between success and failure.
Even in a traditional product like tea, due to globalization, customers will demand consistency, better taste, product differentiation and hygiene in manufacturing and distribution etc. This is actually an opportunity and not a threat. The changed scenario will eventually help the Tea Industry to move up the value chain.
The New Age
In order to cater to the needs of today’s Global customers, the Tea Industry must go through a sea change in their outlook towards the customers. There are no more clear distinctions between the domestic and the export markets. Hence the consistency, quality, hygiene, and the other attributes demanded in the world markets will be demanded in India. There will be a constant pressure on pricing and with open borders; the Indian customers will have access to tea at international prices.
Process Control and Automation the Saviour
Given the above scenario, in order to improve the quality, constancy, and hygiene and in order to reduce the cost of manufacture, the Tea Industry should embrace automation and control wherever possible. In this information age, such systems coupled with the information technology, can provide online monitoring of the process, throughput and a possibility for online information to be available at remote locations.
Plucking
Presently there are a number of automatic leaf cutters available including machines, which are battery operated. This can improve the productivity of the plucking as such as 3 to 4 times.
Field Weighment
Small Handheld Terminals, which can also be used as weighing, balance are available now to weigh the tea leafs and sacks. Optional Smart Card systems enhances the capability of including the information of weights, ration, medicare, wage disbursement etc. This information can be downloaded at the factory to be integrated into the main MIS.
Electronic Weigh Bridge
At the factory gate the Lorry / Tractor, which brings the leaf, gets weighed at the Electronic Weigh Bridge. This Weigh Bridge can be linked to the Central Computer for online information process
Wither Performance Aid.
Withering is a crucial stage in tea processing. This system helps by
• |
Monitoring the temperature and Relative Humidity of the inlet air, so that these could be maintained within the required range to ensure even withering |
• |
Monitoring weight of tea leaves under wither in the sample area, displaying initial/current weight of tea leaves and ratios thereof. |
• |
Correlating wither loss to wither percentage and moisture content using the preset chart. Hence at any point of time the current moisture is indirectly known without even taking sampling. |
The PLC based system can also automatically control the set sequences of operation such as switching the fan on/off, forward or reverse along with hot air or cold air.
Monorail Weighing & Auto Tippling System
To transport the withered leaf from withering trough to shifter the Tea Industries use Monorail. The weighing system incorporated in the Monorail so that the quantity of the withered leaf in every basket as well as the cumulative weight passing through the monorail for a given length of time can be made available. This system has the following advantages
• |
Manpower reduction. |
• |
The weight of the withered leaf going into the process area is available, with breakup of per channel consumption and on hourly rates. |
Elimination of human error and the information can be incorporated in to the total MIS system.
Monorail Weighing & Auto Tippling System |
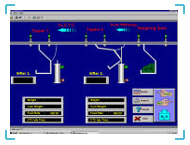 |
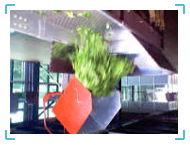 |
Automatic Withered Leaf Feed Regulating Conveyors
In order to regulate the feed of withered leaf into the CTC line through the shredder, rotor vane etc, a conveyorised regulating system is available. This system regulates the flow of withered leaf, so that uniformity is maintained.
This results in not only uniform feeding but also eliminates frequent system failures due to choking.
RC Transportation System
Pulverized RC from the RC room needs to be taken to the CTC line for mixing with withered leaf. By installing a Pneumatic Conveying System using roots blower or centrifugal fan, pipelines, diverters, bag filters and storage silos, RC is transported from the RC room to the storage silos from where it is fed into WL/RC Mix Control System'’. RC can be transported by suction as well as positive phase (blown) methods.
By installing this System the Tea factory has the following advantages
• |
Elimination of dust. |
• |
Better utilization of man power |
• |
Ensuring RC availability at the process line |
Similar systems are also available for transporting RC from the shifting area to the RC grinding room.
WL/RC Controller
The WL/RC controller senses the rate of flow of the withered leaf and gives the feed back to the RC feeding system thus helping the Tea factory to ensure the correct and automatic feeding of RC and adjust the quantity whenever necessary.
The system
• |
Avoids over feeding. |
• |
Ensures consistent mix resulting in consistent quality of Tea fetching better price at auction. |
• |
Better regulation of leaf through chute mechanism and hence even load on subsequent units. |
Fermenting Controller
This is a PLC based Electronic Control System, which is used to control the fermenting process by monitoring and maintaining the temperature inside fermenting drums.
Fermenting Controller |
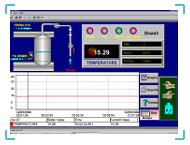 |
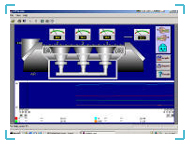 |
The system ensures
• |
That the temperature within the Fermentation drum is kept within the set band of temperatures |
• |
Continuously monitored and recorded for analysis and corrective action. |
Drier Temperature Monitoring System
It is accepted that many of the tea factories may switch over to LPG / GAS based burners for driers. If that happens it is also possible to provide accurate temperature controllers to improve the process.
Material Handling System in the Shop Floor
In order to improve the hygiene, throughput, it is possible to automate the transfer of the CTC Dhool from the Googie to the fermentation process and from the fermentation process to the drier.
Material Handling System in the Shop Floor |
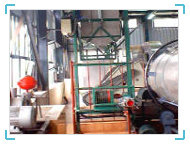 |
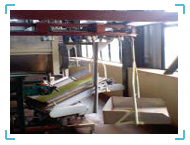 |
Automation in Material Handling in the Orthodox Roller System
In the factories which process orthodox tea, pre weighed withered leaves are transferred to the orthodox rollers. Output of each roller can be automatically transferred to the rollers at the next stage and finally transferred automatically to the fermentation process. In each of the transfers it is possible to weigh the material being transferred, which enables the process and quantity to be monitored accurately.
Drier Output Batch Weighing System
This is a Batch Weighing System controlled by a PLC. It has two vessels with pneumatically operated discharge gates. These vessels are placed one below the other way. The bottom vessel is mounted on set of Load cells. Based on the batch weight fixed, Tea from the drier is received into the top vessel and fed into the weighing vessel below. As soon as the set weight is achieved, the top vessel's discharge gate is closed immediately and the weighing vessel's discharge gate is open after measurement to let the weighed tea out.
Advantages
Accurate weight of drier output and compensates for any particle accumulation
Drier Output Batch Weighing System |
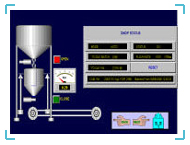 |
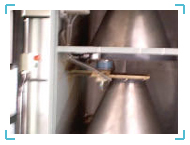 |
Tea Binning and Blending System
Varieties of tea produced are stored in different bins in Tea factories. Handling of the storage process as well as blending the different types of tea grains based on specific recipes can be accomplished by this system. Silos, Conveyors, Vibro Feeders and Blender form the system.
Tea Chest Packing System
These can be simple weighing scales or can be an automated system, based on the need of the factory. There are also totally automated packing machines available for packet tea and for tea bags.
Process Information System / MIS
Since all the systems are controlled by Electronics and are capable of communicating with a central computer, information at every stage of the process is made available. These are then processed to provide the management the required data and analysis / aids in
• |
Monitoring the entire process |
• |
Checking the efficiency of the process |
• |
Calculating the total tea leaf quantity arriving at the factory in a day/month with the information on the field of origin. |
• |
Monitoring the status of the withering at each trough |
• |
Knowing the various grades of tea chests packed |
• |
Reviewing performance |
• |
Report generation, tailor-made to your requirements |
• |
Online mimic, web enabling features. |
The results of introducing these systems are
• |
Consistent Tea Quality |
• |
Higher Price Realization |
• |
Higher Productivity |
• |
On-line Information System |
• |
On-line Process Control |
• |
Energy Saving |
• |
ERP Connectivity |
• |
Web Enabling Possibilities |
|